Sensitization is a phenomenon that can occur in stainless steel. It is a critical concept that needs to be understood as it can adversely affect the performance of stainless steel. This causes the steel or alloy to become susceptible to intergranular corrosion or intergranular stress corrosion cracking (SCC).
What are stainless steels?
Stainless steels are alloys of iron and carbon containing a minimum of about 10.5% chromium and nickel 8%. Stainless steel has a protective layer on its surface that shields it from rust and corrosion. This protective layer is primarily made of chromium oxide and hydroxide (Cr2O3 and Cr(OH)3), which forms naturally when chromium is present in the steel. This oxide layer is extremely thin, invisible, and self-healing, which means that if it gets scratched or damaged, it can repair itself.
The chromium oxide layer is insoluble, compact, and firmly adheres to the steel’s surface. This makes it difficult for water, oxygen, and other corrosive substances to penetrate and harm the underlying steel. As a result, the steel remains free from rust and corrosion, and this is why it is called “stainless” steel. It’s a durable and low-maintenance material that is widely used in various applications where resistance to corrosion is essential.
Chromium is important alloying element in stainless steel which gives basic corrosion resistance property to it. As chromium %age increases the corrosion resistance increases. Although chromium is main element in all kinds of stainless steel grades, other elements are also added to enhance their properties. Nickel is added to promote austenitic structure and also increases ductility and toughness in stainless steel. Carbon is a strong austenite former and strongly promotes an austenitic structure. It also increases the mechanical strength. However, carbon reduces the resistance to intergranular corrosion. Molybdenum when presents substantially increases the resistance to corrosion. Titanium, niobium and tantalum are ferrite stabilizers and strong carbide formers. In austenitic steels they are added to increase the resistance to intergranular corrosion.
Sensitization and Intergranular Corrosion:
Sensitization is the process where chromium and carbon in austenitic stainless steel combine to form chromium carbide (M23C6) particles along the grain boundaries of the steel when exposed to specific temperature ranges (approximately 425 to 850°C), this process is called chromium precipitation also. This process typically occurs when the steel is heated or allowed to cool and allowed to cool through that temperature range at a relatively slow rate, such as during welding, heat treatment, or metal fabrication. Sensitization can occur due to various factors, including improper annealing, stress relieving, or slow cooling through the critical temperature range. It can also happen during heating for welding or forming processes.
During sensitization, carbide particles precipitate at the grain boundaries of the steel. These carbides are rich in chromium, with chromium content as high as 70%, whereas the nominal chromium content in the steel is around 18%. The formation of carbides depletes the surrounding steel of chromium. In the immediate vicinity of the carbides, the chromium content can drop to less than 9%. This reduced chromium content in the steel near the grain boundaries significantly decreases the corrosion resistance of the material. Sensitized stainless steel is prone to intergranular corrosion, where corrosion occurs preferentially along the grain boundaries due to the reduced chromium content in these areas. Microstructures of stainless steel change before and after sensitization, with the latter exhibiting the presence of carbides along the grain boundaries. Sensitization results in the loss of alloy integrity because the sensitized areas have lower corrosion resistance and, therefore, reduced performance in corrosive environments.
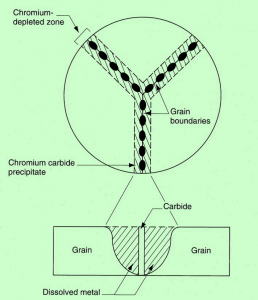
Mechanism of sensitization in stainless steel
What if Stainless Steel is Sensitized?
The extent of carbide precipitation depends upon carbon content, temperature and time at temperature. Sensitization in austenitic stainless steels occurs only in the temperature range 550-850 C. Rapid cooling of the steel through the sensitizing temperature range does not provide adequate time for the process of sensitizing to occur. The rate of sensitization increases with increasing carbon content and decreasing chromium content due to more carbide formation as carbon content increases.
When these sensitized materials are subsequently exposed to aggressive environments, such as acidic solutions, the chromium-depleted regions along the grain boundaries become susceptible to corrosion and the material along with grain boundaries is corroded away. As a consequence, the alloy begins to disintegrate, and in severe cases, the grains may either separate from the steel or become mechanically interconnected, while the material’s stiffness and strength are completely compromised. Any sensitized microstructure is prone to selective localized corrosion along grain boundaries, a phenomenon known as intergranular corrosion (IGC).
IGC is characterized by localized attacks occurring precisely at and near the grain boundaries, with minimal corrosion within the grains themselves. The driving force behind intergranular corrosion is the disparity in electrode potentials between the grain boundary and the grain itself, effectively forming a galvanic cell. In the presence of an electrolyte, the grain boundaries are subject to anodic corrosion. Consequently, alloys susceptible to IGC experience degradation and a reduction in strength when exposed to corrosive environments.
Hence, when dealing with sensitized steel, it’s important to note that the grain boundaries are more vulnerable to corrosion than the rest of the grain. These regions, depleted of chromium, can be selectively dissolved in specific corrosive environments. Intergranular corrosion is prevalent when the carbon content in the stainless steel is elevated or when cooling rates are slow during welding or heat treatment.
In the context of welding, intergranular corrosion arising from sensitization in the heat-affected zone (HAZ), some distance away from the weld, is commonly referred to as “weld decay.” This type of corrosion is typical in non-stabilized steels. In a somewhat distinct scenario, “knifeline attack” represents a localized form of intergranular corrosion occurring closer to the weld zone, typically just a few grain diameters away in austenitic stainless steels. In this case, a narrow band in the parent metal adjacent to the fusion line becomes susceptible to intergranular cracking. Knifeline attack is primarily observed in stabilized grades of stainless steel.
The oxalic acid etch test is a quick observational technique for assessing specimens to identify their potential susceptibility to intergranular corrosion caused by chromium carbide precipitation. This test is typically employed for material acceptance rather than rejection. For a more comprehensive evaluation of susceptibility to intergranular corrosion, tests such as ASTM A923, ASTM A262, and others with similar objectives are frequently utilized when examining stainless steel.
Check our article on IGC test as per ASTM 262
How to prevent sensitization and intergranular corrosion (IGC)?
To address the issue of sensitization and intergranular corrosion in stainless steels, especially during welding, several measures can be taken:
- Utilize Extra Low Carbon Grades: Opt for stainless steel grades with extra low carbon content, such as 304L or 316L, which have carbon levels below 0.03%. This choice ensures that there is insufficient carbon in the alloy to form significant amounts of chromium carbides, thus reducing the presence of chromium at the grain boundaries.
2. Select Low Carbon Base Metal and Filler Metal for Welding: In welding applications, consider using base metals and filler metals with low carbon content. This helps minimize or eliminate the introduction of carbon during the welding process. However, it’s important to note that this may not always be feasible or practical.’
3. Implement Solution Annealing Treatment: Sensitized stainless steel can be restored through a solution annealing treatment. This involves heating the material to temperatures in the range of 1050 to 1100°C, followed by rapid quenching in water. During the heating phase, carbides dissolve, and their reformation or precipitation is prevented by the swift cooling. It’s worth noting that this method may not be suitable for treating large assemblies and may be ineffective when welding is subsequently required for repairs or attaching additional structures.