Regardless of the welding process you use, there are always several factors to consider in order to achieve the best weld quality. From selecting the correct power source to choosing an appropriate filler metal and the most durable gun or torch, each item contributes significantly to the overall success of the application.
But what about other less obvious items that also contribute to weld quality? The X-factor, also called the Bruscato factor, is just such a thing.
Determining the X-factor of a weldment can help prevent defects on several types of materials, but it is especially important to consider when welding chrome-moly steel. This type of steel is commonly used in high temperature applications due to its ability to maintain its strength under such conditions. Additionally, the X-factor directly impacts the filler metals that you should use for such applications. And while it may seem intimidating to learn about at first, understanding and determining the X-factor can help you avoid costly rework and downtime in the long term.
What is the X-factor or Bruscato factor?
The X-factor is a calculation or formula that measures a weldment’s resistance to temper embrittlement-a brittleness or loss of toughness that occurs when the weldment is held (or slowly cooled) through a temperature range of approximately 850 to 1100 degrees Fahrenheit. It is also an efficient and accurate alternative to more expensive testing for this resistance, such as a creep rupture test or a step-cooling test.
It is especially important to know the X-factor when welding certain chrome-moly steels, such as those used for boilers, process piping, steam tubes, heat exchangers, pressure vessels and similar applications that are subject to high service temperatures for extended periods of time. Typical grades of chrome-moly steel to which the X-factor is most relevant include: ASTM A387 Grades, for example, 11, 21, 22 and 91.
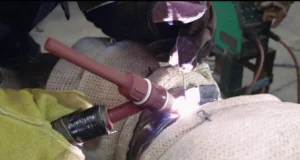
The X-factor measures four elements: phosphorous (P), antimony (Sb), tin (Sn) and arsenic (As). Each of these elements is commonly found (to a certain degree) in the steel portion of filler metals, such as the outer strip of a tubular wire. Together the elements have the greatest impact on a weldment’s susceptibility to temper embrittlement. At elevated temperatures over a period of time, these elements tend to migrate to and accumulate in the grain boundaries of the weldment, weakening its structure. This occurrence results in a loss of ductility and toughness-and eventually causes temper embrittlement. Elements such as silicon can also contribute this problem, but to a much lesser degree.
Calculation of X-Factor
You can calculate the X-factor through a simple formula that multiplies and adds each of the four aforementioned elements in ppm, or parts per million. As long as you know the chemistry of the filler metal that you are using, you will have access to the figures needed to complete this calculation.
The formula to determine the X-factor is as follows:
In this equation, ‘X’ refers to X-factor; 10P refers to the amount of phosphorous in ppm multiplied by 10; 5Sb refers to the amount of antimony in ppm multiplied by 5; 4Sn refers to the amount of tin in ppm multiplied by 4; and As refers to the amount of arsenic in ppm. Once all of these items are multiplied and added together, dividing that amount by 100 provides you with the X-factor for your weldment.
Consider this example for a filler metal with the following amounts of phosphorous, antimony, tin and arsenic measured in weight percent:
P = .007%
Sb = .004%
Sn = .001%
As = .0016%
To determine the X-factor, first, change each percentage to a decimal figure (for example, .007/100 = .00007) and then multiply that figure by 1,000,000 to obtain the ppm. For the phosphorous in this example, the conversion of .0007% results in 70 ppm.
The complete equation in this example would look like this:
X = [(10×70) + (5×40) + (4×10) + 16]/100
The X-factor for this weldment then would be 9.56 ppm
Typically, the goal when welding chrome-moly steel is to keep the X-factor at or below 15 or 20 for as per welding processes. Doing so ensures that you are controlling the amount of phosphorous, antimony, tin and arsenic in the weldment and at the same time ensuring its toughness-or, even more specifically, its resistance to temper embrittlement.
In recent years, there has even been a trend toward maintaining X-factor specifications lower than 15. This trend is due in part to the use of chrome-moly steels for increasingly higher service temperature applications; at higher temperatures, the trace elements tend to migrate easier and can more readily lead to temper embrittlement. High-temperature service applications in colder regions can also benefit from having a lower X-factor, as it ensures better toughness and more resistance to rupture, especially when the chrome-moly steel heats up to temperature.
Nonetheless, never assume that the filler metal you are using for your chrome-moly applications can automatically control the X-factor in your weldment. Not all low alloy filler metals for welding chrome-moly steel have an X-factor below 15, nor are they required to meet this specification. If, however, your application requires temper embrittlement control, remember to complete the X-factor calculation. And, if after calculating the X-factor for your given filler metal, it is above 15, contact your welding distributor or filler metal manufacturer for an alternative product.