Temper embrittlement is a phenomenon in metallurgy where certain materials, particularly alloys and steels, become susceptible to brittle fracture and reduced toughness when exposed to specific temperature ranges. This embrittlement occurs as a result of changes in the microstructure of the material, leading to a decrease in its ductility and impact resistance.
The primary mechanism behind temper embrittlement involves the segregation or precipitation of certain elements within the material’s microstructure. This typically happens during a specific tempering process or when the material is exposed to certain elevated temperatures over time. The embrittled material may appear strong and hard, but it becomes prone to sudden, brittle fractures without significant plastic deformation.
One common example of temper embrittlement is seen in low-alloy steels containing trace amounts of certain elements like antimony, phosphorus, or tin. When these steels are exposed to specific tempering temperatures, these elements can segregate at grain boundaries, reducing the cohesion between grains and making the material more brittle.
In order to assess susceptibility to temper embrittlement in Cr-Mo steels, two compositional parameters are commonly employed, the Watanabe J factor (1) and the Bruscato X factor (2).
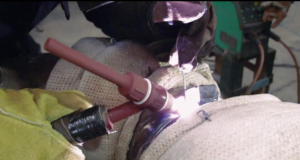
J=(Mn + Si)(P + Sn) x104 (in wt %), has been applied to parent steels and weld metals.
X=(10P + 5Sb + 4Sn + As)/100 (in ppm), is applied to weld metals.
If J is less than or equal to 180, or if X is less than 20, the risk of temper embrittlement is considered to be low. A limit in this form can be specified for procurement, where concerns over temper embrittlement exist.
Step cooling can reveal the susceptibility of a steel to temper embrittlement. The Charpy impact energy and transition temperature for steel after an embrittling heat treatment involving step cooling have been related via a mathematical expression that when fulfilled ensures that the material will not suffer an unacceptable degree of temper embrittlement in service (3).
AF + 2.5(SC – AF) < 38°C
where
AF=As formed Charpy 54J temperature
SC=Step cooled Charpy 54J temperature
This expression is used in the construction of pressure vessels that may operate in the embrittling temperature range, or that may pass slowly through that temperature range upon startup or shutdown.
One step cooling method with hold times and temperatures is given in ASTM A387, supplementary requirements although this gives a more stringent requirement for the acceptable degree of temper embrittlement.
Temper embrittlement has been also related to reheat cracking and low-ductility creep fractures, and a number of types and mechanisms have been proposed, considering carbide precipitation as well as grain boundary embrittling elements.
It’s important to note that the specific mechanisms and susceptibility to temper embrittlement can vary widely depending on the type of material, its composition, and the intended application. Proper understanding of the material’s behavior and careful consideration of temperature exposure are essential in avoiding the negative effects of temper embrittlement.
References
- Ishiguo, T; Murakami, Y; Ohnishi, K and Watanabe, J: “2.25%Cr-1%Mo pressure vessel steels with improved creep rupture strength”; Proceedings of the symposium on Applications of 2.25%Cr-1%Mo steel for thick-wall pressure vessels, ASTM STP 755, 1980, pp. 129-147.
- Bruscato, R. M: “Embrittlement factors for estimating temper embrittlement in 2.25Cr:1Mo, 3.5Ni-1.75Cr-0.5Mo-0.1V and 3.5Ni steels”; ASTM conference, Miami, Florida, 1987.
- Erwin, W.E. and Kerr, J.G: “The use of Quenched and Tempered 2¼Cr-1Mo Steel for Thick Wall Reactor Vessels in Petroleum Refinery Processes: An Interpretive review of 25 Years of Research and Application”; WRC Bulletin 275, February 1982.
- ASTM A387:”Standard specification for pressure vessel plates, Alloy steel, Chromium-molybdenum”
- 🧠 API 580 RBI Quiz Questions for Inspectors
- Complete Guide to Welding Duplex Stainless Steels (P No. 10H)
- The Rise of Collaborative Cobots in Welding and Fabrication
- Radiography Quiz – Questions, Answers, and Explanations
- Weld Joint Strength Reduction Factor (W)