What is Heat Input (HI):
In arc welding, energy is transferred from the welding electrode to the base metal by an electric arc. When welder initiate the arc, the welding electrode and base metal is melted and weld pool is generated. This weld pool results due to the energy supplied through the power source. Energy supplied to the weld per unit of length is called arc energy. When arc energy is multiplied with process efficiency it is termed as heat input. Heat input in welding is important when comparison between different processes is to be done. But when comparison between processes is not to be made and only control over the welding parameters are required arc energy is generally treated as heat input. In ASME codes arc energy is referred as heat input because it refers for controlling of welding parameters not for the comparison between different welding processes. We have provided heat input importance in next parahrapgh.
Importance of heat input:
Many reference and construction codes refer for the controlling of heat input in welding during procedure qualifications and further in production also. In general, heat input control is required where impact or corrosion resistance properties are required. ASME section IX also includes heat input in supplementary variables means when the impact testing is required means you have to keep control over welding parameters related to heat input when impact is specified for the weld.
The important characteristic of heat input is it governs the cooling rate of the welds and therefore effects the microstructure of the weld. It is similar to the preheat, when the heat input in welding is increased the cooling rate of the weld is decreased. Slower cooling rates results in coarser grain size in the weld and HAZ and effects the mechanical properties(specially toughness) of the weld. Coarser grain size of weld and HAZ results in less no. of grain boundaries exhibits less toughness, so it is required to control heat input when toughness properties are to be meet in weld and HAZ.
Heat input Calculation:
Arc energy and heat input both are measure of how much energy is supplied to work piece per unit length. To calculate heat input we have to first calculate arc energy and then multiply arc energy calculation by thermal efficiency of the process for which heat input in welding is to be calculated
Arc Energy (AE):
Arc energy is the energy supplied by the power source to the workpiece i.e.
Arc Energy Formula; AE = VI*60/T.S
Where
V is the voltage used, in volts
I is the current used, in amperes
T.S is the travel speed of the welding electrode, in distance per minute (mm/min.)
Units of are Arc Energy is J/mm.
Heat Input Calculation In Welding(H.I) :
We will discuss how to calculate heat input in welding
Heat input is the actual energy reaches to the workpiece it’s calculated by multiplying the thermal efficiency of the process to the arc energy.
Welding Heat Input formula (H.I.) = ɳ*AE
Welding Heat Input Equation/ Heat Input formula in KJ/mm = VI*60/T.S*1000
Heat input units : J/mm & KJ/mm
Where
AE is arc energy in J/mm
ɳ is the thermal efficiency of the process which has no units and is dimensionless.
Thermal efficiency for the different arc welding process are tabulated below
Welding Process | Thermal Efficiency |
Gas Tungsten Arc Welding (GTAW) | 0.6 |
Shielded Metal Arc Welding (SMAW) | 0.8 |
Flux Cored Arc Welding (FCAW) | 0.8 |
Gas Metal Arc Welding (GMAW) | 0.8 |
Submerged Arc Welding (SAW) | 1.0 |
Metal Cored Arc Welding | 0.8 |
Plasma Arc Welding (PAW) | 1.0 |
Other methods to calculate heat Input are listed in ASME Section IX are described below
- Heat Input determined by instantaneous energy/power : Method defined above are useful for DC welding with where welding parameters are not rapidly can be averaged easily but in waveform controlled weld the heat input cannot be calculated by above mentioned formula due to rapidly-changing outputs, phase shifts, and synergic changes. During waveform controlled welding, current and voltage and values observed on the equipment meters no longer are valid for heat input determination, and must be replaced by instantaneous energy (joules) or power (joules/second or watts) to correctly calculate heat input. For example GMAW-P welding waveform controlled power sources are used. Such welded power source generally shows instantaneous energy or power if not shown by power source external equipment can be used for measuring instantaneous energy or power. Welding power sources or external equipment shows instantaneous energy as a cumulative measure of instantaneous energy ie the sum of instantaneous energy measurements made during a time period such as trigger-on to trigger-off. The units of measurement may be joules (J) or any other equivalent. If machines are not giving instantaneous energy then below formula against total power/energy given by welding power source or external equipment can be used
(i) Heat input for instantaneous energy measured in Joules (J)
= Energy (J)/ Weld Bead Length (mm)
(ii) Heat input for instantaneous power measured in Joules (J)
= [Power (J) * Arc Time(S)] / Weld Bead Length (mm)
2. Volume of weld Deposit: As per ASME section IX instead of heat input we can be calculate the volume of weld metal deposited per unit of length of weld for each process. The volume of weld deposited can measured by following methods
(i) By measuring the size of bead i.e. width * Thickness of the weld bead
(ii) By measuring the length of weld per unit of electrode
Examples for heat Input formula in welding & heat input calculation:
Example 1: You are using conventional power source welding machine and using GTAW arc welding process. The parameters used for welding showing on machine are current 125A and voltage 13V. 250mm of length is welded in 4 minutes of time. What will be heat input?
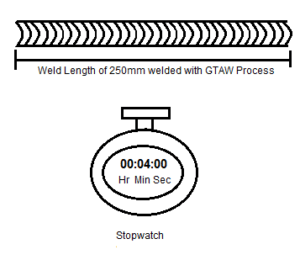
First you have calculate travel speed before calculating heat input by applying below mentioned formula
Travel Speed (T.S.) = Length of Weld/ Time Taken to weld = 250mm/4 minutes = 62.5mm/minute
Heat Input (H.I.) = (V*I*60)/T.S. = (13*125*60)/62.5 = 1560J/mm
Example 2: You are using a special waveform on a power source with GTAW process. The reading on the display for energy used for length of 500mm is 560J. What will be heat input?
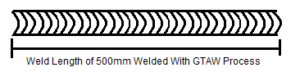
No need of calculation of travel speed for calculating heat input in this method. We just need to put formula.
Heat Input welding(H.I.) = Total Energy (KJ)/ Weld Bead length = 560 KJ/ 500mm = 1.12 KJ/mm = 1120KJ/mm.
You can use our heat input calculator & above explained heat input formula for welding for calculating heat input
Heat Input Calculator
Good nice contribution
Very good
Simply explained… commendable work…please provide some article on supplementary essential variables from section IX…
Knowledgable explanation
Nicely explained
Easy and clear explanation for heat input calculations.
Very informative and explained well.
Any effect in heat Input in weld if we change the groove detail of weld joint .
Heat Input depends upon travel speed, current and voltage. There is no any affect in heat input by changing groove detail and joint design.
Highly appreciable
Really excellent explain .
Thanks so much
Nicely explained,
Good job Abhishek
Good pawan yadav
Pawan sharma oman
Good job abhishek and very nice explain. thanks so much .
Hii
Hello
Heat Input, weld energy: well explained. Appriciate your efforts, thanks for sharing the information